Whena motor burns out, do you rewind it or replace it? Back in Issue 3 of Smart Energy User we introduced this important topic, and here andin our next issue we explore some of the key questions in more detail.
- Induction Motor Rewinding Calculations
- Induction Motor Rewinding Calculation
- Induction Motor Winding Calculation
Sometimes — for one of the reasonsdiscussed in this article — the obvious best approach is to rewind themotor. If the magnetic core of a failedmotor is undamaged and appropriate procedures are followed, a rewound motorwill retain its original efficiency. Properly repaired, a “standard” efficiency motor will have its original“standard” efficiency, and an energy-efficient (EE) motor will have itsoriginal high efficiency.
On the other hand, those times when amotor has failed are also opportunities to upgrademotor efficiency. Especially if thefailed motor is 10 or more years old — perhaps with unknown efficiency, andpossibly having been improperly rewound in the past — you will want toseriously consider all the options,and look into the economics of replacing it with a new EE motor.
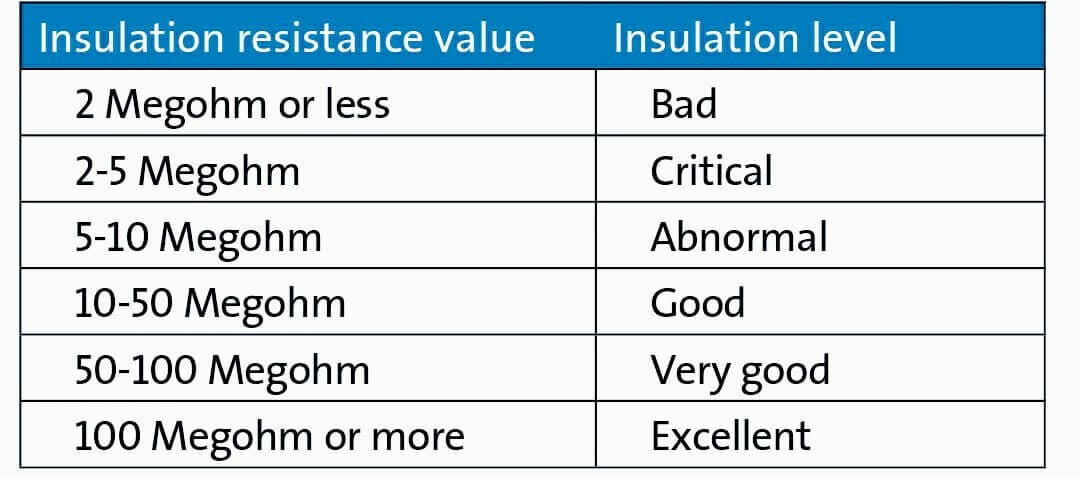
Induction Motor Rewinding Calculations
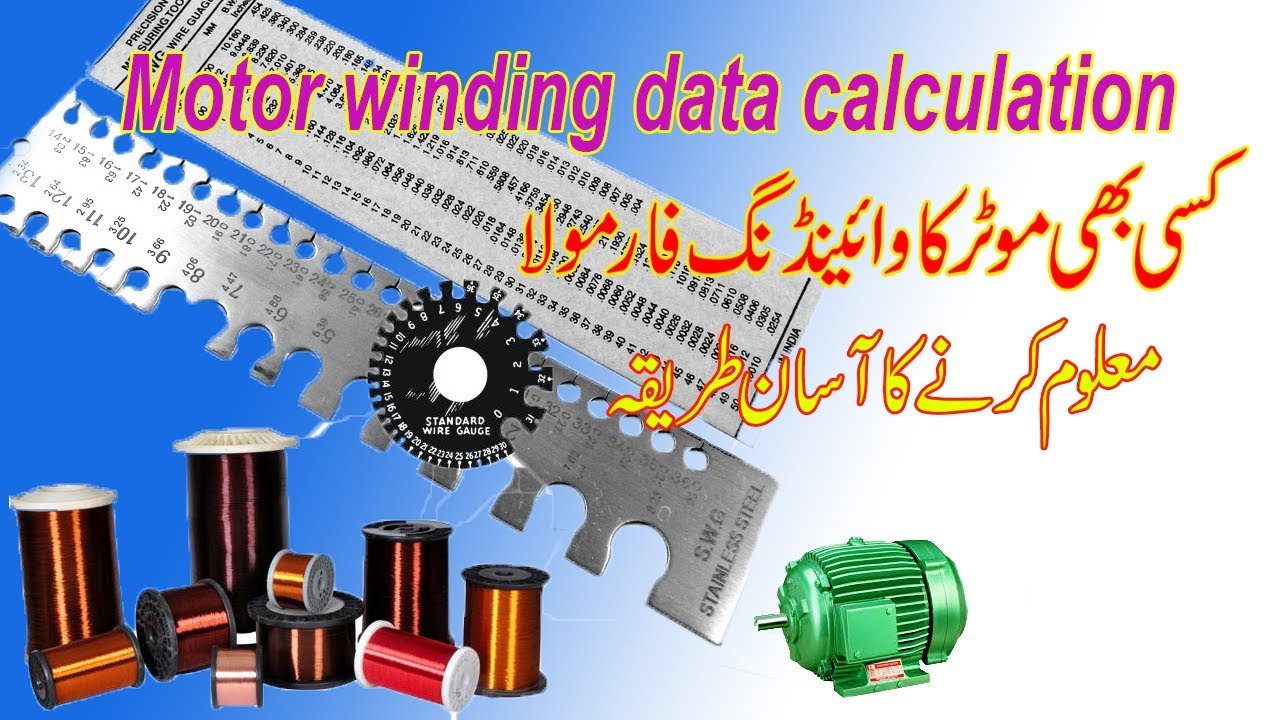
THE PAYBACKISSUE
- The calculation will be performed for the air-cooled, three-phase motors for continuous duty cycle S1, standard efficiency, 50 or 60 Hz, SF 1.00, lap or concentric, single or double-layer, for the maximum power from the given iron core. Please, carefully review the information needed, and be aware that more details gives more accurate results.
- Principle-of-three-phase-induction-motor/ Per-phase equivalent circuit. Motor Slip. R 1 and R 2: stator and rotor winding resistances. X 1 and X 2.
- The winding calculator allows you to find the optimum winding layout for your electric motor in a fast and convenient way. You can investigate three-phase integer-slot, fractional-slot and concentrated windings, both with single and double winding layers where appropriate.
- The calculation will be performed for the air-cooled, three-phase motors for continuous duty cycle S1, standard efficiency, 50 or 60 Hz, SF 1.00, lap or concentric, single or double-layer, for the maximum power from the given iron core. Please, carefully review the information needed, and be aware that more details gives more accurate results.
For experimentation, as a rule of thumb for a single phase, I normally start with 7, 8, 9 Turns per volt per square inch of laminated area available. Try it with 8 turns per volt per square inch, wound over the two opposing poles.
The more horsepower a motor delivers, andthe more hours per year it runs, the greater the operating cost and the moreimportant the motor’s efficiency turns out to be. Small motors, and motors that are used infrequently or only forshort periods, don’t cost a lot to run even if they are inefficient. But when a large horsepower motor operatesfor thousands of hours per year, the operating cost is substantial. And, that motor’s efficiency can have asignificant effect on the company’s bottom line.
If a standard efficiency motor has failed,you face
adilemma: Should you spend x dollars tohave the motor rewound, and keep the operating cost the same — or potentiallyhigher? Or should you spendsignificantly more than x dollars for a new EE motor, and reduce the operating cost? It is possible to arrive at rational answers to these questions by doingsome simple calculations. For informationon how to do this, see the article in the last issue (Issue 17), Calculating What it Costs to Run a Motor,and the article in our next issue (Issue 19), Easy Comparison of Motor Cost/Payback Options. (If you don’t have copies of these issues,call us.)
STATOR COREDAMAGE
Induction motors employ an armature that rotates within a fixed stator, with a small air gap between thetwo. A typical motor stator is shownbelow.
Induction Motor Rewinding Calculation
Induction Motor Winding Calculation
Itconsists of a core of stacked, insulated, iron laminations, with windings ofinsulated copper wire